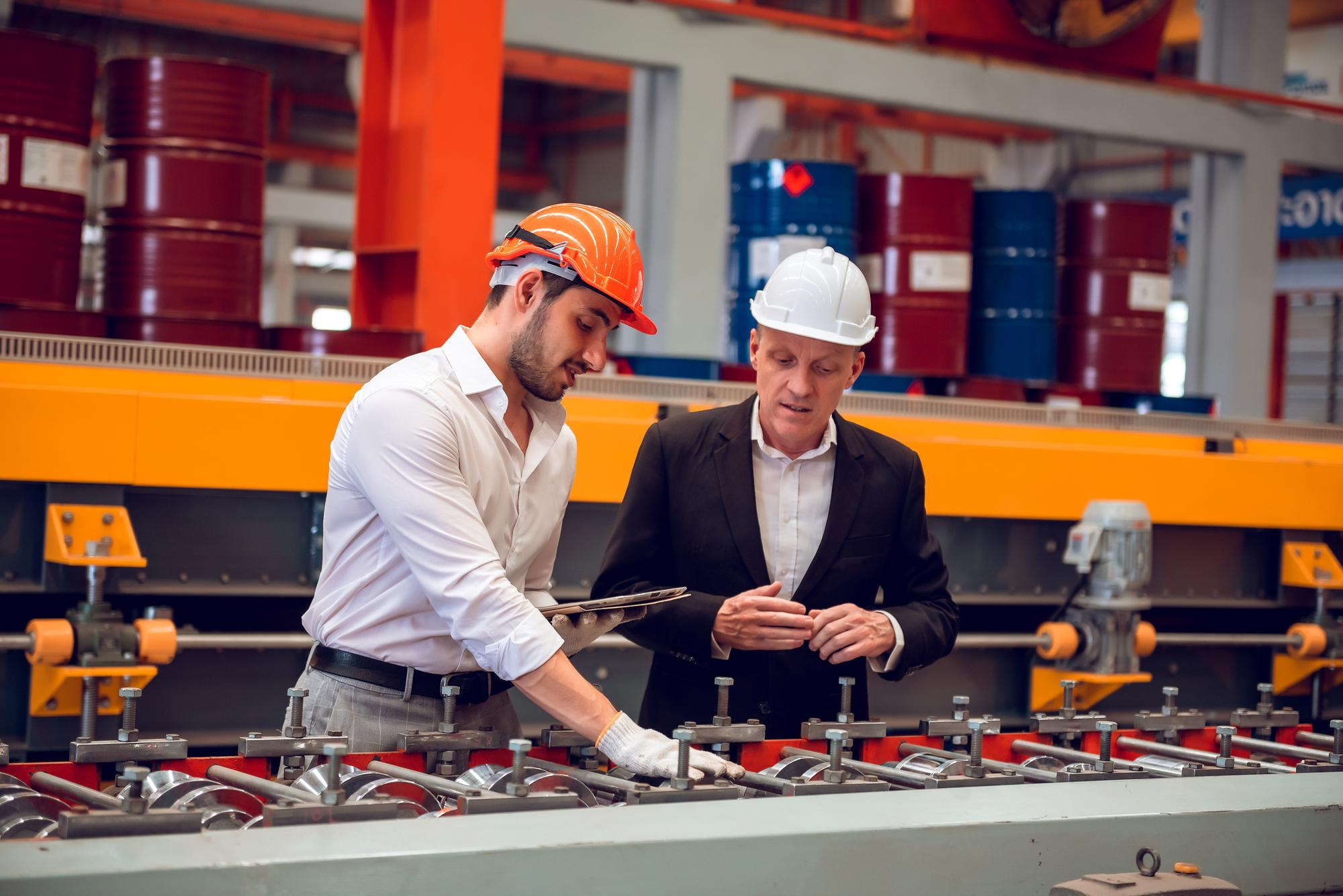
Technology consulting in industrial sectors
We invite you to familiarize yourself with our full offer in the following industries:
Aluminum die casting
We are the sole distributor of MotulTech - Baraldi in Poland in the field of aluminum die casting technology, which has over a hundred years of tradition and sets trends on the market in this area. Our Partner's advantage is having a Technical Center where new chemicals are developed and tested for high-quality and environmentally friendly production.
The key analysis of the application, which is the basis for the search for new materials, formulations and innovative solutions, is developed directly by Baraldi's in-house Research Centre. This enables the creation of state-of-the-art products that comply with environmental protection regulations (according to ISO 9001 and ISO 14001 standards). Special equipment allows the assessment of thermal parameters, ability to form coatings and adhesion to the surface of various products. This data is analyzed in laboratories and can be used to collaborate with our customers and to develop new products.
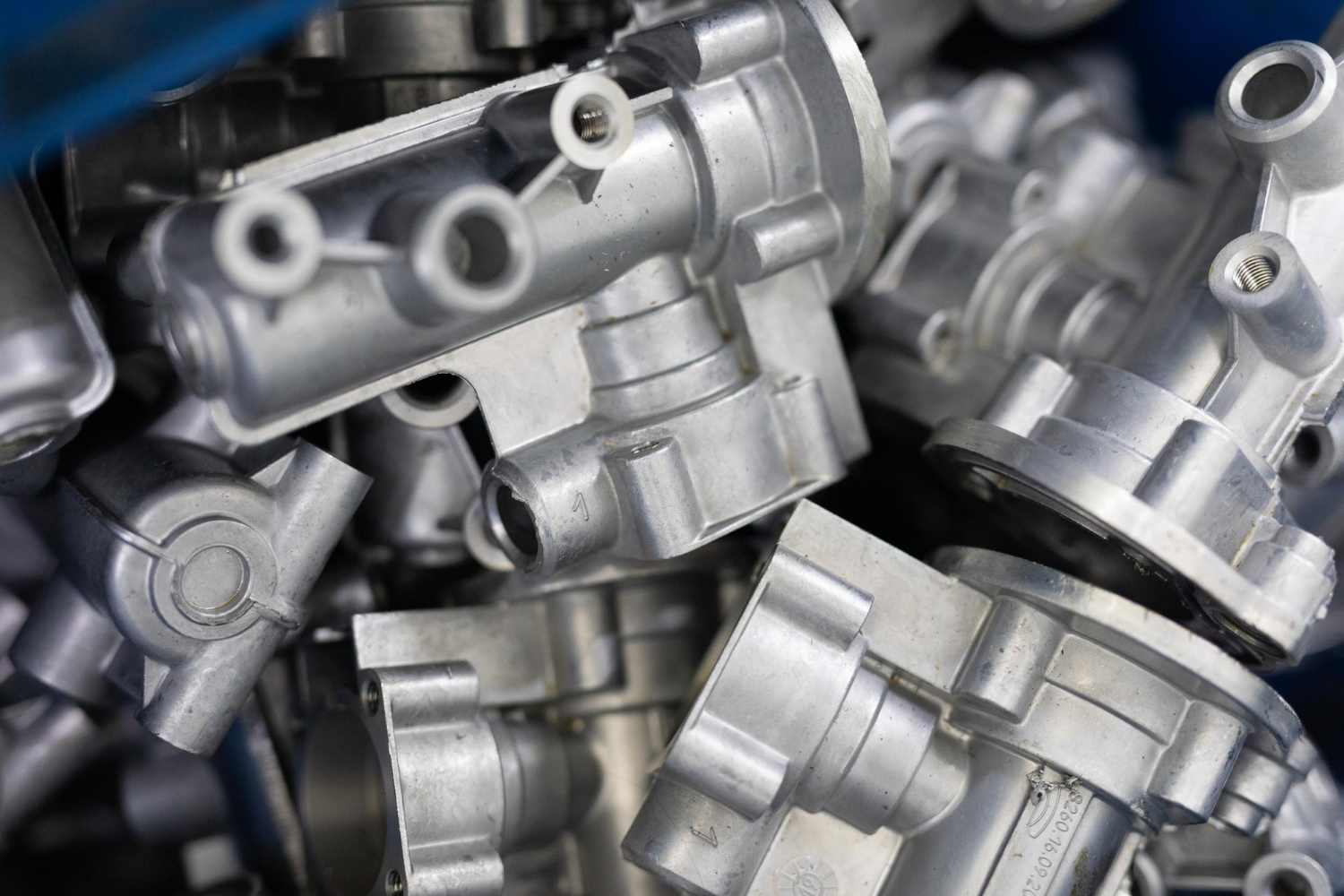
We have at our disposal TTV (TOTAL THERMAL VISION) infrared vision technology that monitors the thermal map of the mold surface in real time. Developed by MotulTech-Baraldi and well established in the field, TTV technology is the ideal instrument to increase quality and productivity in the die casting process, also for high production rates.
Description of the optimization process:
- Collection of data from one or more machines via TTV camera systems or manual camera;
- Data analysis in iCast Lube Analyzer to suggest process improvements (application, concentration, spray time);
- Defining goals with the client;
- Execution of tests using TTV cameras in order to OPTIMIZE the process;
- Preparation of a test report and summary of the results;
- Defining new projects.
Objective:
- Ensure good separation
- The mold and all its parts must be lubricated
- Mold surface thermal balance, mold agent is the last tool to balance the surface temperature
- To help the metal slide, the agent layer on the mold is the medium between the mold surface and the injected alloy
- Protects the mold, the separator is a "protective cream" that we spread on the surface of the mold to protect it
- The product provides detail finish
- CASTING TTV is designed to increase productivity
Forging
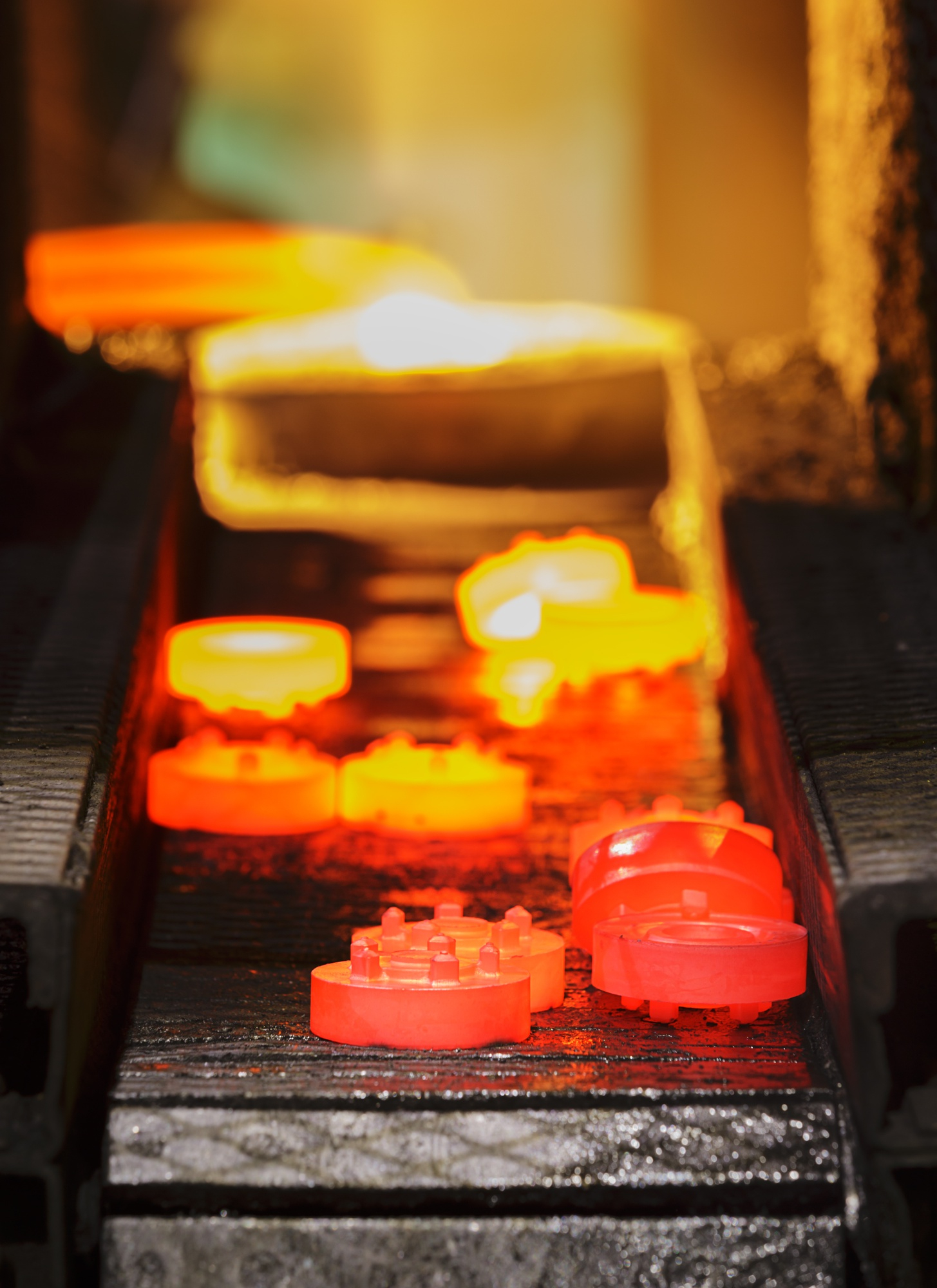
In hot forging steel technology, the most common lubricant/separating agent is based on an aqueous dispersion of graphite where the water cools the tool and assists in spraying the agent onto the mould. In more complex, demanding applications, especially with materials such as aluminum, bronze, brass, nickel, titanium, water-immiscible graphite agents are used. In this case, the graphite can be dispersed in the oil, this combination meets the high performance requirements of the lubricant.
There are also applications in which we use graphite-free agents. These products are based on biodegradable salts, provide a clean working environment, do not clog nozzles, and there is no need to mix the solution afterwards.
We invite you to contact our engineers in order to choose the right product.
Profile production
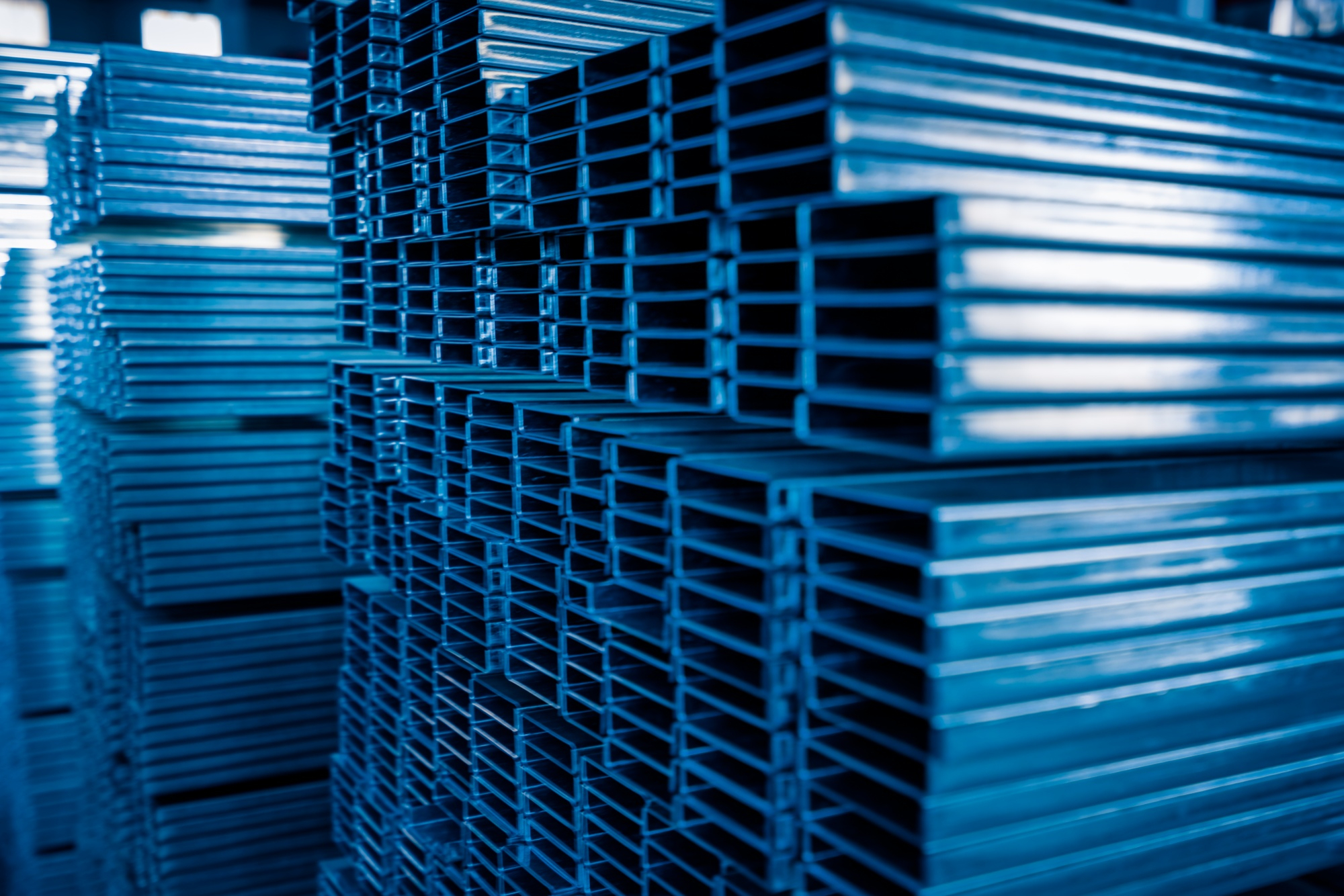
Our technological solutions during the production of profiles reduce or completely eliminate the formation of "red" or "white" corrosion at a later stage. This applies to profiles made of hot and cold rolled and galvanized steel. Weather conditions, formation of moisture and emulsion (pH, concentration, corrosion protection) are crucial in the process.
We also know how important the surface quality of the finished product is for the customer, which is why our solutions ensure high cleanliness and aesthetic appearance of the profiles. We recommend using appropriate solutions that clean the profile of scale, emulsion, other oils, filings and other impurities.
We use appropriate anti-corrosion agents, depending on the customer's requirements. They leave a dry or wet oil film, displace emulsions and moisture from the profiles. We recommend appropriate devices that spray the anti-corrosion agent in the optimal amount.
During cooperation, we offer technical advice in the implementation of our solutions.
Our goal is to reduce or completely eliminate the phenomenon of corrosion.
Machining
A properly selected cooling and lubricating fluid, commonly known as a coolant, has a significant impact on the proper functioning of machines and tools. In addition to cooling and lubricating properties, anti-corrosion properties, compatibility with processed materials, air release, foam resistance, washing properties, heat transfer, lubricating properties, long emulsion life, stability during operation, no health hazard and others are very important.
Industrial plants are looking for more and more efficient coolants, they want to minimize the frequency of failures, reduce repair and service costs, which are an important part of all operating costs of the plant.
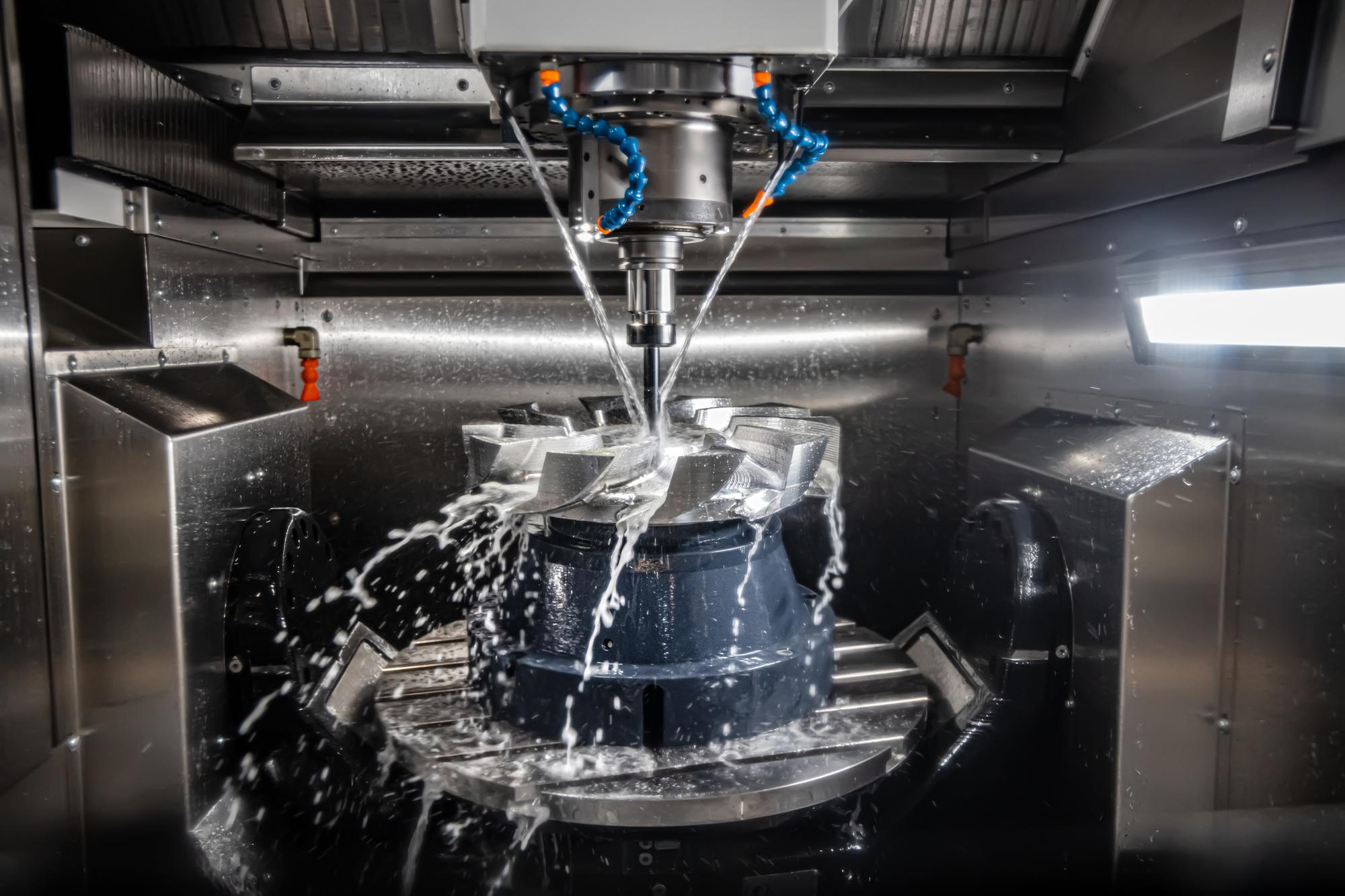
The most common on the market are coolants based on mineral oil. Such emulsion liquids, in addition to mineral oil and the necessary emulsifier, also contain corrosion inhibitors or anti-foaming additives and others. Mineral oil, unfortunately, is not always welcome in production plants, because it causes difficulties with its removal and subsequent painting. It is also an easy breeding ground for microorganisms (fungi and bacteria), which in turn causes an irritating smell in the workplace, irritation of operators, soiling of machines. These factors lead to the destruction of the emulsion.
BB TECHNOLOGY, together with its partners, implements emulsion liquid technologies without mineral oil content. The products in this line bear the name COOLTUBE. They have a significantly extended service life and are biostable compared to mineral oil-based solutions.
These products are a Polish brand and are produced in Poland.
Choosing the right coolant requires qualified technical support. Service care is another important aspect after product implementation.
BB TECHNOLOGY offers full cooperation in the field of the correct selection of process fluid and after-sales care, including tests of parameters such as concentration, hardness, pH, chlorides, foreign oil content and others.
Plastic processing
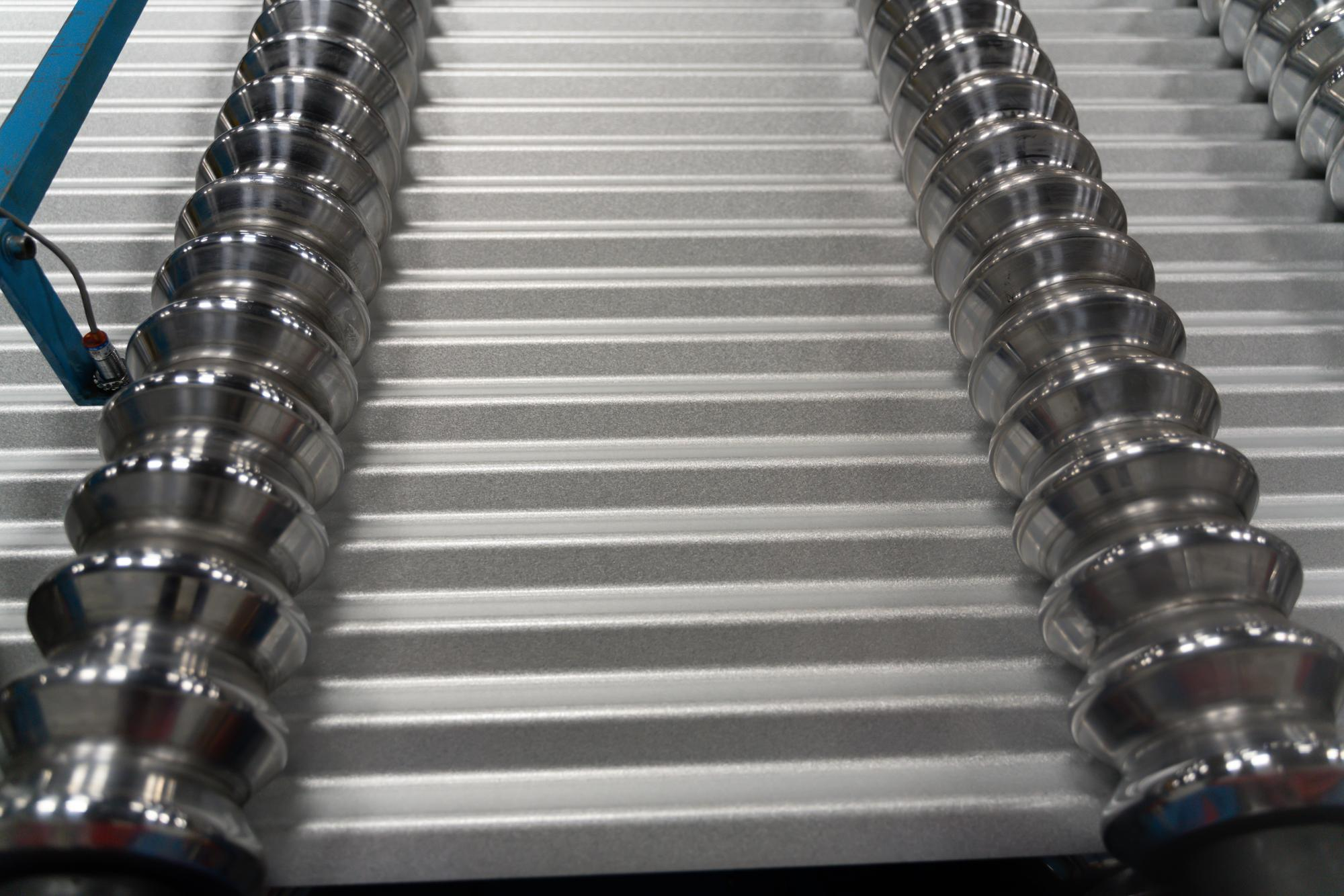
Selection of a plastic forming agent requires knowledge not only of the appropriate technical application (type of metal, sheet thickness, type of operation), but also of further processes such as anti-corrosion protection or detail washing. With a properly selected lubricant, the washing process or additional protection can be eliminated.
Also important aspects are the subsequent welding, brazing, welding processes, in which the lubricant must be compatible.
For machine operators, the following are important: no hazardous fumes, no irritating odors and a clean workplace.
BB Technology, in addition to the selection of the appropriate agent and service care, also offers appropriate devices with a minimum lubrication system to minimize the use of the product.